“Concern for man himself and his safety must always form the chief interest of all technical endeavor. Never forget this in the midst of your diagrams and equations.”
~Albert Einstein
Each industrial revolution has ushered in transformation in the industry in many different ways. With transformation, the lives of the workforce have also changed dramatically, not just monetarily. New safety measures have been introduced from time to time to keep the workers safe at workplace. Working conditions and labour laws, too, have improved considerably. While many industry stalwarts have advocated the importance of safety at workplace by investing in advanced safety gear, more often than not, the novelty of wearing shining PPE (Personal Protective Equipment) wears off as the worker gets comfortable with the work environment. A colossal effort from the supervisor and the management is needed to keep things in order when it comes to maintaining safety and preventing loss of work days. A positive safety culture will translate to positive morale of the workforce leading to improved quality and productivity. This will also ensure employee retention.
Why PPE?
Any training on workplace safety clearly states why safety procedures are important for employees, especially in manufacturing plants that handle toxic gases and chemicals, cutting and grinding machines and heat treatment installations. Importance of protective gear is communicated through visual aids and live demonstrations to ensure complete understanding of the risks and dangers. Needless to say, safe environment translates to higher work days and protective gear has a large part to play in it. It is up to the organization how it manages to ensure that workers understand this too.
Familiarity breeds contempt?
On interviewing workers from all age groups and experience levels, the most common answer received from the majority was, “I am so familiar with the task that I can do it blindfold! Why then should I wear this safety gear? The gear slows me down.”
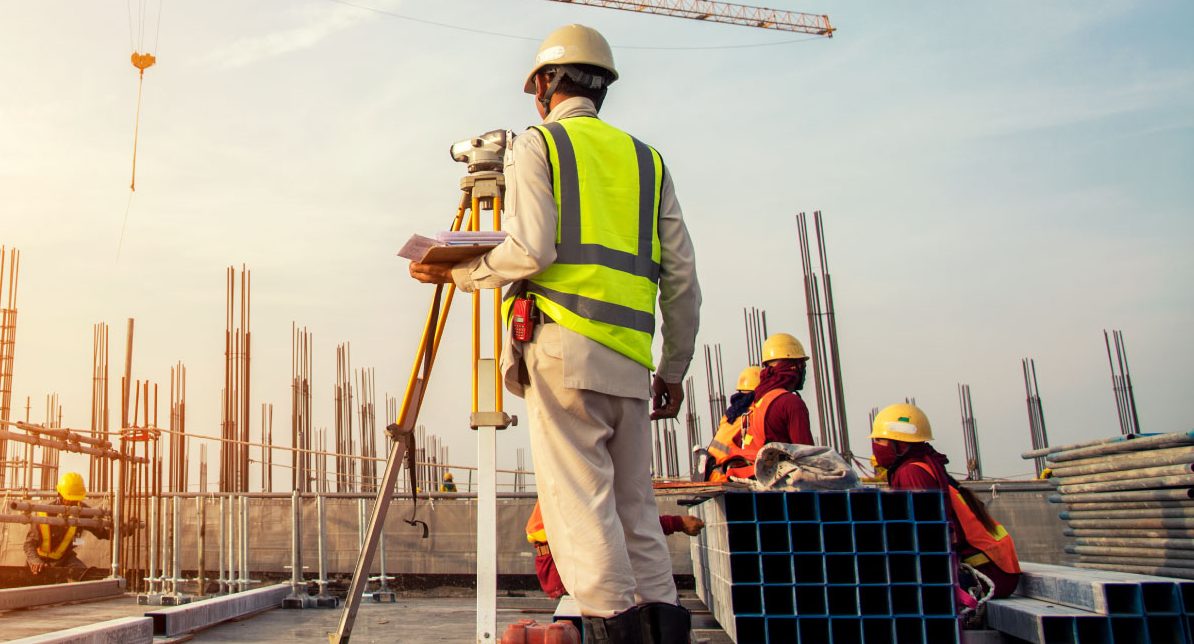
So, how to turn this complacency and ignorance into cautiousness and discipline?
One way to achieve this is through periodic training at multiple levels with a top-down approach. A continuous cycle of effective trainings will help create awareness on how to properly wear PPE, besides drilling in the importance of wearing the gear while working in hazardous spaces. While plant managers and supervisors need training to introduce and manage a safe environment, shop floor workers should be motivated to adhere to it with the right training.
Practice makes perfect!
The benefit of training lies in its frequency. Besides the usual training scheduled as per company policies, supervisors and managers should make it a regular topic of discussion at daily meetings. Senior leaders, too, need to interact with shop floor staff to bridge the gap. This is when one-on-one discussions will help the employee get answers to individual queries from experienced staff. Moreover, when they are listened to, they are more likely to listen to their supervisors in return. Purpose of these discussions is to ensure every worker knows how to use PPE correctly to make use of the gear effectively and not come in the way of worker efficiency. Employees will comply with safety procedures only when they understand the usage and risks thoroughly.
The right motivation
Instead of punishments and penalties for non-compliance, the organization should advocate positive reinforcements to achieve sustainability and productivity at workplace. For instance, if the workers understand that by wearing PPE they are actually contributing to safety of the plant, they will be motivated to follow the rules without being under undue pressure caused by fear of punishment.
Adherence to safety protocol cannot be brought about with just a one-time training on policy compliance. It is a steady and ongoing process that requires nurturing at various levels. Involvement of supervisors and managers is key to the success of creating a safe and positive work culture by turning a rule into a way of life.