Toy manufacturing has the potential to create millions of jobs. With the right policy support, a target of a $2-3 billion market by 2024 can be achieved to generate a whopping 2-3 million direct jobs.
By Amit Chakraborty, President, Toys Business Segment, Aequs.
It has been a year since Prime Minister (PM) Narendra Modi’s Mann Ki Baat on toys stirred up a fragmented industry that was highly dependent on China for survival.
His call for “vocal-for-local” signalled a focus on toys for the domestic market, urging businesses to look at India’s history in traditional toys for inspiration. His subsequent address to the industry at the first Toycathon-2021 in June was a further boost to the “toyconomy”, bringing in export opportunities to India’s toy story.
Even though India’s shot at the global toy market predates the PM’s initiative, it brought about a flurry of expressions of intent and spate of actions from various quarters. The present momentum has the potential to reap a globally competitive industry creating millions of job opportunities in this labour-incentive sector.
Yet, a lot of potential remains unlocked, without a focused end-game strategy, with key low hanging fruit not being harvested.
The China story
Of the $100 billion-odd global toy market, India accounts for just $1.5 billion annually. About 80% of this is met through imports, mostly from China. Of the global sourcing value of $30-40 billion, China’s contract manufacturers have almost 70% of the pie, with Vietnam accounting for the lion’s share of the balance. Mexico and India are upcoming challengers to this equation. Some brands have legacy manufacturing in Indonesia and Malaysia, and tactical sourcing in Turkey, Brazil and east Europe.
It took over three decades for China to reach this pinnacle, as it built mega ecosystems to cater to the entire supply chain for manufacturing toys.
China’s toy and gift capital, the Chenghai district in Shantou city, Guangdong province, is one such ecosystem. Spread across 345 square km, Chenghai hosts over 5,000 units that are said to account for 30% of the world’s toys. Other major production centres in the Guangdong province include Shenzhen, Dongguan, Guangzhou, and Foshan cities.
December 18, 1978, marks an important transition in China’s history and the start of the Boluan Fanzheng period during which it opened up its economy. It ushered in industry-favourable policies to attract global supply chains and talents to China. The toy industry, which was then largely based out of Hong Kong, moved out en masse to China.
Within a decade, Hong Kong reinvented itself to be a design and development centre. Large American and European brands set up their sourcing offices in Hong Kong, which to date, are the all-powerful deciders of the fate of sourcing supply chains.
Hong Kong industrialists and brands transferred manufacturing technology to the China factories that churned out toys at a fraction of the cost in the United States (US) or Europe. It was a win-win game for all partners in the chain.
Apart from building scale, Chinese manufacturers moved up the value-chain, adding technological capabilities and expertise to encapsulate the entire supply chain.
The potential in India
However, change is the essence of progress, and as China moved towards becoming a developed nation, the cost advantage it long enjoyed was waning. Vietnam surged due to its proximity to China and capital inflows.
However, with a limited labour pool and the simultaneous influx of many industries into Vietnam, the country’s long-term prospects in the toy industry remain limited. Chinese entrepreneurs are moving on to the production of high value, high technology toys.
This is where India can step in.
India’s demographic advantage is its greatest asset, with labour rates being a third of China’s and half of Vietnam’s. This needs to be bolstered with proper skill development and labour policies in consonance with growth mindsets as opposed to archaic socialist mindsets.
However, some critical parts of the supply chain continue to reside in China. The big brands, with their outsourcing overdrive, do not have any manufacturing capabilities to transfer. India must use its engineering and entrepreneurship skills to develop these supply chains.
Industry associations and governments must create linkages with global networks to influence decision-making. This will have to be backed with flawless service delivery creating a positive flywheel.
The role of the State in nourishing this is paramount in creating a global level playing field through equitable incentives and targeted force multipliers such as exports.
Despite progress, the speed of administrative decision-making and the quality of basic physical infrastructure remain key concerns for India. Further, entrepreneurship in India, which has been traditionally skewed towards the software industry, small-to-midsize manufacturing, and trading, needs to realign towards mass manufacturing.
“The traditional and modern toy factories need to coexist in the value chain”
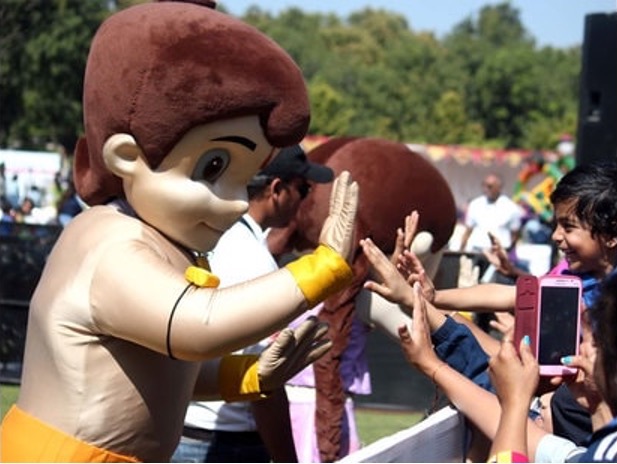
Toy making is not child’s play: Focus on scale
Compared to the 5,000-plus units in just China’s Chenghai district, India boasts of just about 4,000 units, mostly in the unorganised sector. This fragmented nature of the Indian toy sector works against it.
That toy making is only a small-scale, cottage industry-oriented activity is a myth. Scale economics play a big role in not only attracting global original equipment manufacturers (OEMs) and brands, but also building a sustainable domestic market supply.
Further, toy making is not child’s play. It is a confluence of art and science, demanding high and nuanced low-cost precision engineering, and technical skills, along with experienced aesthetic sensibilities.
Though entry barriers may seem low, the confluence of low-cost engineering with the supply chain, continuous technology upgrades, product development capabilities, design and tool-making capabilities, skilled labour force and State focus, need to fall in place together for the industry to fire at a global scale.
China’s ecosystem is a networked environment, where expertise and scale have been built by various partners as a focused part of the supply chain. India needs to adapt and configure mid-sized integrated ecosystems to quickly get capabilities in place.
The ripple effect of toy clusters
There is a likelihood that multiple toy clusters will be announced. But building an ecosystem in the clusters is a tall order, and would require a purposeful long-term approach.
The Koppal toy cluster — India’s first modern toy cluster — coming up in north Karnataka is one such ecosystem building an entire value chain of capabilities. With co-located global scale assembly and pack out capacities, a 400-acre toy unit is on its way — a mini-Chenghai, if you will.
With the projected investment of ₹7,000 crore over the next decade, the 400-plus acre integrated manufacturing ecosystem will provide end-to-end Toy development and manufacturing capabilities. It will house over 100 large and small manufacturing units in the special economic zones (SEZs) for exports, and domestic tariff area (DTA) for the domestic market. It will provide direct employment to over 25,000 people.
India’s toy story can support more toy clusters provided they do not get into a mix of land hoarding and real estate play, under the guise of manufacturing.
It will be an uphill task for the industry to develop such citadels of excellence without the right policy support and incentive mechanism. For instance, while the Government of India has rolled out the National Toy Action Plan, the proposals need specifics on each element of the toy manufacturing value chain.
Likewise, the much-talked-about Production Linked Incentive (PLI) scheme, despite being available to 13-plus sectors, does not cover the toy industry. Export incentives such as the Merchandise Exports from India Scheme (MEIS) have been withdrawn with no viable alternatives in place.
Stop toying around
Toy representation continues to be a subpart of the sports goods industry and therefore lacks any focus in decision making. Policy skew towards traditional and low-capacity manufacturing will not create scale economics for India to emerge as a global force.
Additionally, carte blanche import duties are not a panacea for domestic manufacturing. The critical raw material supply chain is starved, and toys that complement our capacities lose out on an economic commercial opportunity.
The traditional and modern toy factories need to coexist in the value chain. Traditional manufacturers could very well occupy low-volume, higher-margin speciality toys, whereas the large ones could be taking on the world.
The key to “homegrown” toys is not just about traditional manufacturing, but creating home brands such as Chota Bheem and exploring that intellectual property to create world-class toys in modern toy factories.
The toy sector has a huge potential to create jobs. For every $10 million generated in revenues, the industry has the potential to create 1,000 direct jobs, not including the downstream employment. With the right policy support, a $2-3 billion capacity is achievable within a short period. This will lead to a whopping 2-3 million jobs. To put this in perspective, the entire Indian information technology (IT) industry employs only 4.6 million people.
A focus on developing India’s toy sector at a faster pace, with the right policies, infrastructure, and entrepreneurship, can transform India’s economy and social footprint.
This opinion piece was first published in Hindustan Times on Oct 22, 2021, 06:35 PM IST